Logistics is one of the most well-known corporate services. If you run a logistics company or work as a logistics business manager, keep reading because this article will provide you with the best ideas on optimizing your company to make the most of it.
Plan Ahead:
Managing seasonal peaks and labor demand must begin with planning. For all logistics companies, planning is essential for navigating the busy season. Year-round planning is required to guarantee that the team is fully prepared for peak season. Logistics managers may avoid unforeseen frustrations by planning to control customer delivery expectations.
Planning for Increased Workforce Requirements:
We all know that planning entails various tasks, including budgeting, purchasing things, storing them, contracting and negotiating with suppliers, and delivering items. The main goal of planning is to do the most work in the least amount of time while maximizing profits.
As a result, proper preparation allows you to be prepared for the unexpected and address any difficulties. It also assists you in reducing or eliminating supply chain delays.
Logistics managers must prepare ahead of time for their workforce requirements. They must decide how many shifts they will need to operate during the high Christmas season and how many temporary workers they will hire. They must also consider an incentive scheme and bonuses for employees to keep them pleased throughout the increased seasonal workload.
Setting Order Deadlines in Advance:
Logistics Managers could plan to shift order deadlines a day or two before the festival day to prevent last-minute stress and create more reasonable delivery expectations for consumers.
Planning for Exceptions:
Logistics managers should consider designating a handling area for handling exceptions such as shipments that exceed the volume and weight restrictions of handling equipment, products that require special handling, and orders that cannot be fulfilled. Handling unique situations in their location might help keep item delivery flowing quickly during the holiday season.
Using a fulfillment center for your business:
Fulfillment centers, also known as third-party logistics businesses (3PLs), are an excellent way to increase your fulfillment capacity. A fulfillment center performs all order processing for you if you run an e-commerce merchant selling items on an e-commerce platform. They will receive the order, prepare it for shipping, and deliver it to the customer.
When a consumer places an order, the information is transmitted to a third-party logistics provider (third-party logistics provider) or fulfillment center. Because your inventory is already in storage at the center, they accept the order, gather the purchased things, and package them. The order is subsequently delivered to the buyer by a shipping carrier. It’s the same procedure, but it relieves you of the stress and, in many situations, gets the job done faster and more efficiently.
A fulfillment center completes orders quickly, efficiently, and affordably. Fulfillment centers can handle both business-to-customer (B2C) and business-to-business (B2B) orders. B2B orders are often delivered to a shop, whereas B2C orders are delivered to the customer’s house.
Investing in Good Packaging Material:
Product packaging, at its most basic level, helps safeguard the product within. Packaging must protect the goods throughout transit between the production site and the store and shield the items on the shelf. As a result, product packaging must be durable and dependable. Many firms package their products with seals and locks to prevent tampering and to further assure the product’s safety and integrity. Consumers want their items to work as they should—secure, dependable product packaging is the best way to achieve that.
Tracking your Shipments:
As your company expands, you will require more resources and effort to maintain current standards. The greater the number of orders, the greater the demand for skilled personnel for delivery, and, as a result, the profit margins will increase significantly.
Success and advancement imply several delivery trucks, more skilled delivery people, and more unprecedented or sophisticated runs in the business environment. The tracking system for cars and delivery personnel must be comparable in this case. To boost the efficiency of your business in this digitalized age, you must keep your clients up to date at all times. These changes include a visual tracking system that allows consumers to see the shipment process from when the order is placed to the completion of delivery.
It can help you understand the organization’s successful management while keeping your clients pleased with your business. When it comes to company optimization, the tracking system is crucial. If your company is focused on delivery and you want your consumers to be completely satisfied, a tracker is a requirement.
Staying Organized:
It’s critical to examine your business frequently to ensure that you’re on the correct route. Inventory management is an essential component of every organization.
By efficiently managing your inventory, you can have the correct items in the right number on hand while avoiding out-of-stock products and cash being locked up in excess stock. You may also guarantee that your items are sold on time to minimize spoiling or expiration and overspending on goods in a warehouse or stockroom.
Keep an Eye on the Budget:
You should be aware of how much each component of the logistics process costs you, rather than focusing on the larger ones such as shipping or packing. When you know where each dollar, euro, or pound is going, it is much easier to pinpoint areas where you can cut expenditures and keep your cash flow under control.
Backup Plan: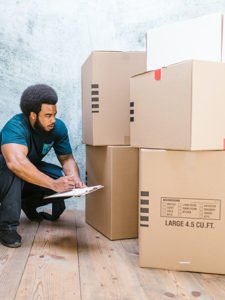
An interruption in the supply of products and services on which your firm relies can be disastrous to the business. To help keep operations going smoothly, address supply chain and inventory management methods and backup plans for business before an issue arises.
Here are some things to think about:
Secondary Suppliers:
If your most crucial suppliers’ components, materials, commodities, or services are unavailable, you should know what to do.
Delivery on Demand:
Check with your suppliers to see if they can make special arrangements to fill and deliver orders on dates or locate someone who can.
Notify Important Customers:
You rely on your supplier, and your consumers depend on you. If crucial orders are delayed, tell the consumers who will be affected.
Create a Supply Chain Management Strategy:
Supply chain management should be addressed in your strategic and business continuity plans. Create and record measures to assist defend against disruptions in delivering your most critical inventory and services.
Logistics is a critical component of the supply chain and your overall business operations, and it can make or break it. These seven logistical tips might assist you in ensuring that everything runs well.